Plant Shutdowns and the External Workforce
Plant shutdowns are a necessary part of maintaining and upgrading industrial facilities. These planned outages allow for necessary maintenance, inspections, and upgrades to be performed, helping to ensure the safe and efficient operation of the plant. However, managing contractors during a plant shutdown can be a complex and time-consuming task.
Â
Challenges in Plant Shutdowns
Â
One of the main challenges of managing contractors during a plant shutdown is coordination. With multiple contractors working on different tasks simultaneously, it’s important to have a clear plan in place to ensure that everyone is working towards the same goals and that there are no conflicts or delays. This requires careful planning and communication, both before and during the shutdown.
Â
Another challenge of managing contractors during a plant shutdown is safety. Industrial facilities can be dangerous environments, and it’s crucial to ensure that all contractors are following proper safety protocols. This includes providing proper training and equipment, as well as monitoring and enforcing compliance with safety regulations.
Â
Cost Management
Â
Managing the cost of contractors is also an important consideration during a plant shutdown. The cost of labor and materials can add up quickly, and it’s important to have a budget in place and to monitor expenses to ensure that the project stays within budget. This can be a challenging task, especially when dealing with multiple contractors and unexpected issues that arise during the shutdown.
Â
Communication
Â
Effective communication is key to successful management of contractors during a plant shutdown. Clear and regular communication between the plant management and the contractors is essential to ensure that everyone is aware of the goals, schedule, and budget for the project. It also helps to identify and resolve issues as they arise, preventing delays and keeping the project on track.
Â
Plant shutdowns are a necessary part of maintaining and upgrading industrial facilities. However, managing contractors during a plant shutdown can be a complex and time-consuming task. Coordination, safety, cost management, and effective communication are all important considerations that must be taken into account in order to ensure a successful shutdown.
Â
Benefits of Digitalization
Â
Contractor management software can help with plant shutdowns by providing a centralized platform for managing and coordinating all activities of contractors involved in the shutdown process. This can include features such as scheduling and tracking the progress of work, managing safety and compliance, and communication tools to keep all parties informed and on the same page.
Â
Additionally, contractor management software provides a record of all activities, which can be useful for post-shutdown analysis and planning for future shutdowns.
Â
By being proactive and having a clear plan in place, plant managers can minimize disruptions and keep the project on schedule and within budget.
Â
About NHD
Â
For over 20 years, NHD has been providing an intelligent, all-in-one solution that bridges the gap between your company and your external workforce in the full source-to-pay cycle.
Companies using the AES/32 contractor management platform by NHD experience:
- Integrated communication processes with suppliers; from demand to payment
- Quotation process supported by approved unit rate catalogues
- Effective time management with integration into gate systems
- Provides 100% contract compliance through standardized catalogues
- Dynamic auditing for process and rate compliance
- In-depth reporting and analytics for fatigue management, earned value management, contractor/site performance, and more
- Seamlessly integrates with SAP ERP/S4/Hana and more
Let's Chat.
Discover how our software is transforming contractor management. Contact us today.
5,000+ successful deployments with companies like you.
AES is a cloud-based platform for labour and service procurement enabling clients and suppliers to seamlessly collaborate throughout all stages of project planning to payment for asset intensive operations.
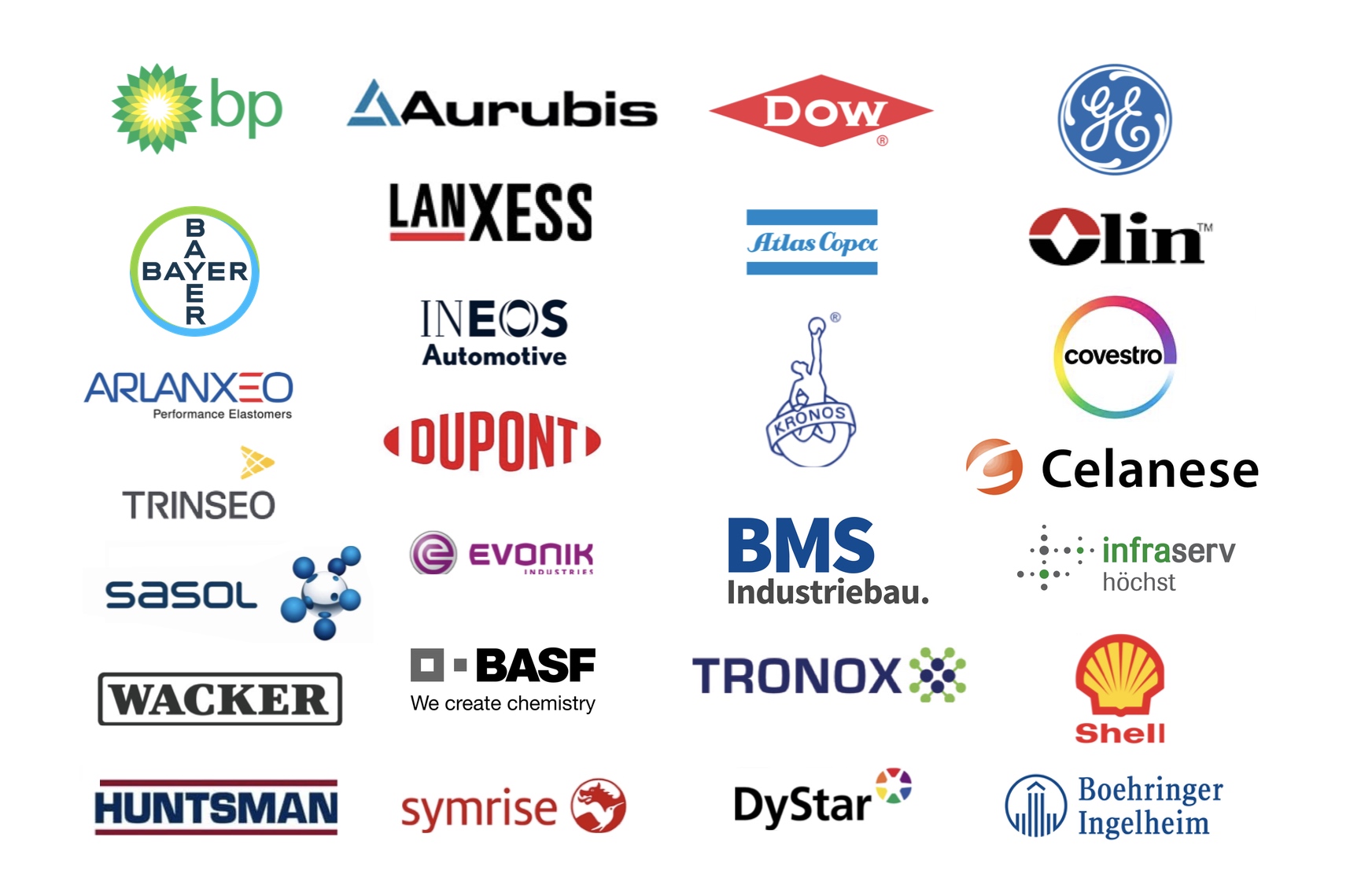